Canwell Medical is open for visitors! So you are probably wondering what a tour to Canwell factory will be like. And as a green Canweller, I’m glad to say that my first tour as an intern was one of shock and awe. The amount of effort we put into each section is at the factory simply remarkable. Now join me as I take you on this tour to the Canwell Land.
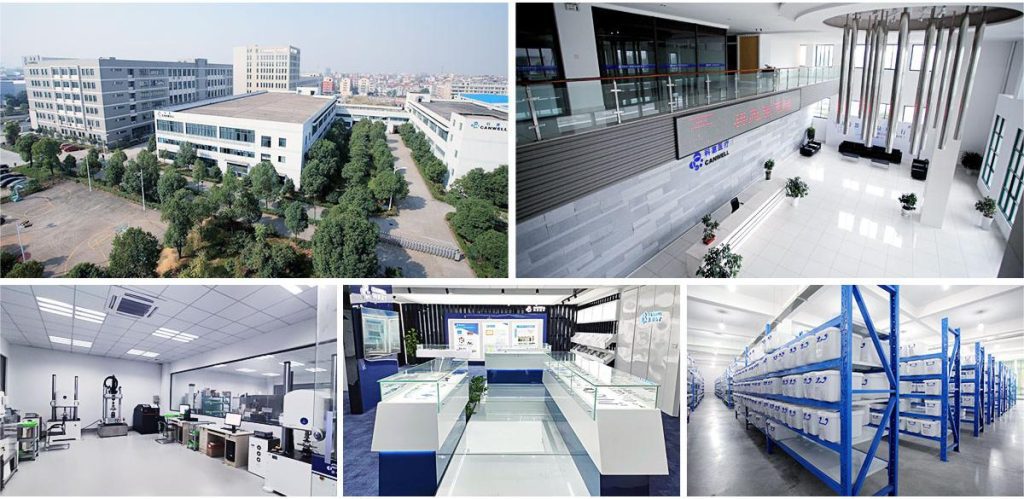
First Stop – Exhibition Hall: Company History, Global Reach, Partnership, and Product Samples
The exhibition hall is where your factory tour begins. Here, you will learn about the history of Canwell Medical, its global reach, and partnerships with other leading companies in the medical device industry. You’ll also have the opportunity to see samples of Canwell’s products and gain a clear understanding of each product’s application
Canwell Medical’s commitment to innovation and excellence has earned the company a global reputation for providing high-quality medical devices and implants. The company’s products are used by medical professionals in over 50 countries around the world, including partnerships with Zimmer Biomet and Smith&Nephew.
Second Stop – Canwell IT Department: Traceability and Privacy
Canwell Medical’s IT department is one of the most powerful and secure in the industry. The department ensures that all files related to products and transactions are safely stored with backup copies in Canwell’s servers at home and overseas. This helps to ensure the traceability of products and the privacy of the Canwell’s clients.
Third Stop – Canwell R&D Center: Fatigue Test, 3D Printing, Aging Test, Physicochemical Test, and PhD R&D Center
Canwell Medical’s R&D department is a hub of innovation and creativity, constantly pushing the boundaries of medical device development. The department is responsible for designing and testing all of the company’s products, ensuring they meet the highest standards of quality and performance.
The fatigue test is one of the critical tests that all of Canwell Medical’s products must undergo. Spine products go through five million times of F1717 bending fatigue test for two weeks, while trauma products go through one million times of fatigue test for two days. Cages go through axial compression experiments to ensure that they are strong enough to withstand the rigors of daily use.

Canwell Medical’s R&D department also uses 3D printing technology. It helps design ideas materialize, paving the way for innovation and customization. Additionally, the department conducts aging tests that ensure the durability of products, including plastic packing that must endure for at least 97 days. Physicochemical tests are also conducted to analyze the chemicals in raw materials, ensuring the highest levels of purity and quality.
Canwell Medical’s PhD R&D Center is working closely with Zhejiang University on its future product line. This partnership helps to ensure that the company’s products remain at the forefront of medical device development.
Fourth Stop – Canwell Clean Room: 100,000/300,000 Level Clean Room; Patent Wall: Showcasing Canwell Medical’s Innovation
The clean room is where Canwell Medical’s products are assembled and packaged. The clean room is a 100,000/300,000 level clean room. The particulate count in a 300,000-level clean room is typically limited to no more than 300,000 particles per cubic foot of air. This level of cleanliness is suitable for many manufacturing processes, including the production of electronic components, semiconductors, pharmaceuticals, and medical devices. To achieve this level of cleanliness, the room is equipped with advanced air filtration and air handling systems that continuously circulate and purify the air. These systems typically use a combination of HEPA (high-efficiency particulate air) filters and ULPA (ultra-low particulate air) filters to remove particles as small as 0.1 microns in diameter.
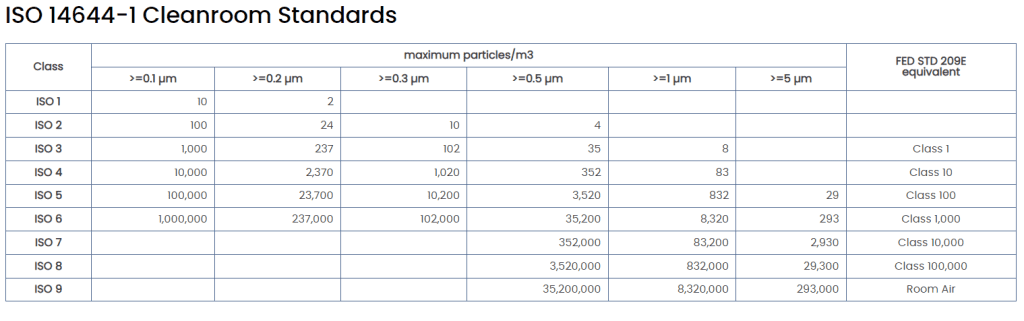
Canwell Medical takes great pride in its commitment to innovation and excellence. The company’s patent wall showcases its most significant innovations. Visitors will have a glimpse of the company’s creativity and ingenuity.
Fifth Stop – Canwell Pure Water System: Rough Cleaning and Fine Cleaning
Canwell Medical’s products must be thoroughly cleaned before they are packaged and shipped to customers. The pure water system is used for both rough cleaning and fine cleaning.
Sixth Stop – Second Floor Hallway Overlooking the Workshop: Imported Equipment from Germany, Japan, and Switzerland
As you move through the factory tour route, you’ll make your way to the second floor hallway overlooking the workshop. Here, you’ll see the state-of-the-art equipment that Canwell Medical uses to manufacture its products. The equipment is imported from Germany, Japan, and Switzerland, ensuring that the products are of the highest quality.
Seventh Stop – Second Floor – Instrument Workshop: Plate, Rod, Wire Cutting, Processing, and Tolerance
The instrument workshop is where Canwell Medical’s products are manufactured. The workshop is equipped with the latest plate, rod, and wire cutting and processing equipment, ensuring that the products are manufactured to the highest standards. The tolerance level for Canwell’s products is 0.02, which is significantly lower than the industry standard of 0.2. This ensures that the products are of the highest quality and precision.
Eighth Stop – Canwell Instrument Warehouse: Semi-Finished Product and Finished Product
The instrument warehouse is where Canwell Medical stores its semi-finished and finished products. The warehouse is organized and managed efficiently, ensuring that the products are stored correctly and are easily accessible when needed.
Ninth Stop – Canwell Implant Shop: Processing Machines and Raw Material
The implant shop is where Canwell Medical’s products are processed and prepared for packaging and shipping. The shop is equipped with advanced five-axis machines, rip cutting machines, and slow-feeding wire-cut machines. The raw material used to manufacture Canwell’s products is 455/630 imported stainless steel, ensuring that the products are of the highest quality.
Tenth Stop – Post-Processing: The Final Stage of Product Development
Post-processing is the final stage of Canwell Medical’s product development process. This stage involves inspecting, cleaning, and packaging the products before they are shipped to customers. Canwell Medical’s commitment to quality is evident in the way it approaches post-processing, ensuring that every product is inspected and cleaned to the highest standards.
Final Stop – Canwell Reception Room
So you’ve seen what Canwell’s factory looks like. Now join me to the reception room for some tea and refreshments. And we can shake hands and get the business done!
Canwell Medical is a leading manufacturer of medical devices and implants, with a commitment to innovation, excellence, and quality. The factory tour route provides visitors with a comprehensive overview of the company’s history, global reach, partnerships, and product development processes. From the exhibition hall to the clean room, visitors will gain insight into the company’s dedication to producing high-quality products that meet the highest standards of performance and safety. If you’re interested in learning more about Canwell Medical and its products, we encourage you to visit the company and experience the factory tour route for yourself!